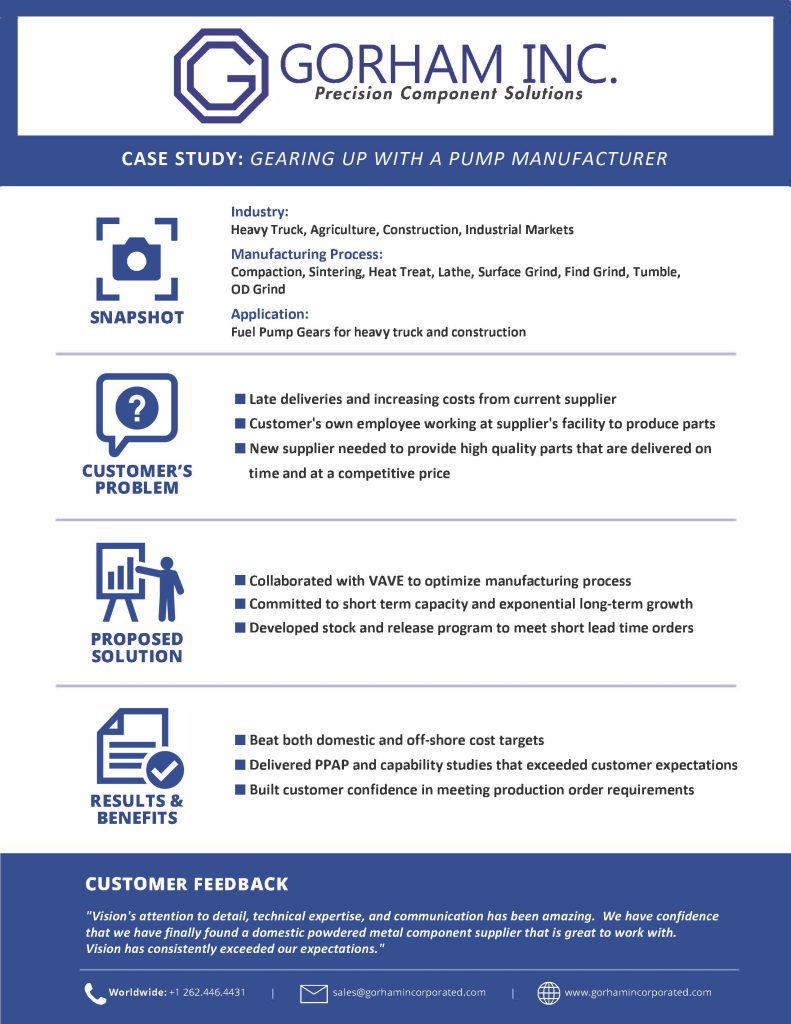
May 4th, 2022
Your Source for both Screw Machining and Swiss Screw Machining
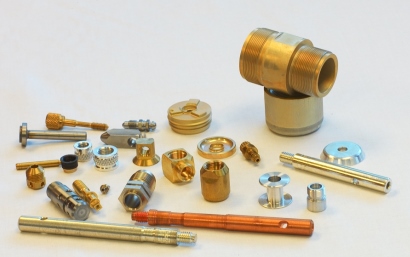
SCREW MACHINING is the process of rapidly spinning lathes that shave metal down to the desired size. There are 2 major types of screw machines: Turret and Swiss. Both processes are able to perform more precise work as a byproduct of their tight configuration and tooling. Swiss screw machines are superior to Turret style machines in their ability to output more precise work due to their ability to add additional types of tooling fixtures.
CNC SWISS SCREW MACHINES provide the ability to deliver the small, high precision parts necessary for the manufacturing of critical components. Swiss screw machining is perfect for close tolerance and complex parts, and is capable of running different grades of metal and plastic. CNC Swiss screw machines allow engineers to explore different options to improve performance and reduce cost, while achieving a high level of detail and precision. |
Please let us know how we can help you with your Screw Machining needs!
We have OPEN CAPACITY for Custom Rubber Molded Seals
March 25th, 2022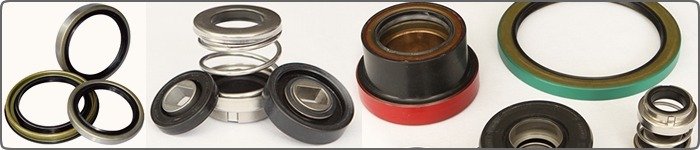
We provide the most advanced custom seal designs, application engineering, and problem seal analysis in the industry. We are a highly specialized seal engineering firm, and precision manufacturer of elastomeric seals for OEM and the oil & gas industry. Contact us for a quote today!
Custom Plastic Injection Molding plus Standard Knobs & Handles
July 29th, 2021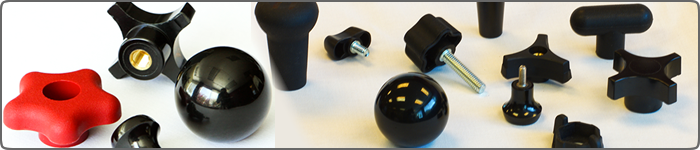
Superior product quality and breadth of molding capabilities allows us to deliver high performance custom plastic components and a superior line of knob and handle products. Local engineering and local molding, coupled with high quality die construction, allows us to be a leader in the plastic molding industry.
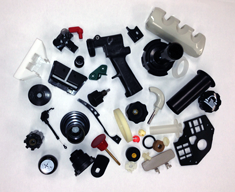
Custom Rubber Molding and Bearings
June 29th, 2021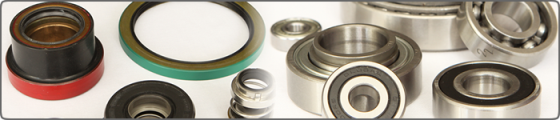
Providing the most advanced custom seal designs, application engineering and problem seal analysis in the industry, we are a highly specialized seal engineering firm, and precision manufacturer of elastomeric seals for OEM and the oil & gas industry.
In addition, we are a supplier of the highest quality, ISO certified bearings, with focus on solutions, pricing and delivery.
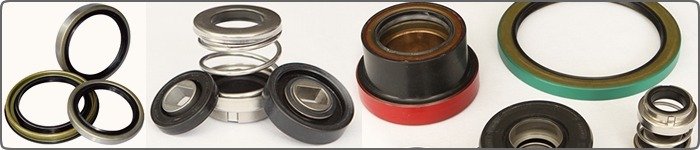